Курсовая работа: Производство керамзитобетонных однослойных панелей наружных стен
Требование к
керамзитовому песку:
К песку, предъявляются
требования в соответствии с ГОСТ 9757:
Зерновой состав песка
должен соответствовать указанному в таблице 5.
Таблица 5
Зерновой
состав
Размер
отверстий сит, мм
|
5 |
1,25 |
0,315 |
0,16 |
Менее 0,16 |
Полные
остатки на ситах, %
|
0 |
20-60 |
45-80 |
70-90 |
10-30 |
В песке применяемого в качестве заполнителей для
армированных бетонов, содержание водорастворимых сернистых и сернокислых
соединений в пересчете на SO3 не должно превышать 1% по массе.
Песок, предназначенный для приготовления
теплоизоляционных и конструкционно-теплоизоляционных легких бетонов, должны
подвергаться периодическим испытаниям на теплопроводность.
Требования
к керамзитовому гравию:
Крупный
заполнитель – керамзитовый гравий, марка керамзитового гравия по насыпной
плотности – 500, марка по прочности П125, плотность зёрен в цементном тесте γз.к.
фракции 5-10 мм – 1,25 кг/л, фракции 10-20 мм – 1,19 кг/л.
Требования к керамзитовому
гравию представлено в таблице 6:
Таблица 6
Требования к керамзитовому
гравию
Наименование
показателя |
Норма
|
Прочность |
По марке по прочности
П125 |
Насыпная плотность |
По марке насыпной
плотности 500 |
Плотность зёрен |
Фр. 5-10 мм – 1,25
кг/л;
Фр. 10-20 мм – 1,19
кг/л.
|
Содержание пылевидных и
глинистых частиц |
Не более 2% по массе |
Содержание глин в комках
– 0,5%; |
Не более 0,5%; |
Влажность |
ГОСТ 8736-85 и ГОСТ
10218-85 |
Требования к воде:
Вода для приготовления
бетонов должна удовлетворять требованиям ГОСТ 23732.
Для приготовления
бетонной смеси используют водопроводную питьевую, а также любую воду, имеющую
водородный показатель рН не менее 4 (т. е. некислую, не окрашивающую лакмусовую
бумагу в красный цвет).
Требования к воде указаны в таблице 7:
Таблица 7
Требования к воде по ГОСТ
23732
Наименование
показателя
|
Норма
|
Содержание ПАВ не более, мг |
10 |
Содержание
сахаров и фенолов не более, мг |
10 |
Содержание окрашивающих примесей,
жиров и масел |
Не допустимо |
Показатель рН, не менее |
4 |
Содержание сульфатов, более |
2700 мг/л |
Содержание всех солей, более |
5000 мг/л |
цех керамзитобетон панель сырье
4. Технологическая часть
4.1 Обоснование технологической схемы производства
Рассмотрим две
технологические линии по производству стеновых панелей: стендовую и
конвейерную.
Конвейерное производство – усовершенствованный поточно-агрегатный способ
формования наружных стеновых панелей. При конвейерном способе технологический
процесс расчленяется на элементные процессы, которые выполняются одновременно
на отдельных рабочих постах.
При конвейерном способе, формы с изделиями перемещаются от одного поста к
другому специальными транспортными устройствами, каждое рабочее место
обслуживается закреплённым за ним звеном. Для конвейера характерен
принудительный режим работы, т.е. одновременное перемещение всех форм по
замкнутому технологическому кольцу с заданной скоростью. Весь процесс
изготовления стеновых панелей разделяется на технологические операции, причём
одна или несколько из них выполняются на определённом посту.
Тепловые агрегаты являются частью конвейерного кольца и работают в его системе
также в принудительном режиме (ритме). Это обуславливает одинаковые или кратные
расстояния между технологическими постами (шаг конвейера), одинаковые габариты
форм и развёрнутую длину тепловых агрегатов.
Оборудование конвейеров рассчитано на изготовление определённого вида
изделий.
Конвейерный способ обеспечивает высокую степень механизации и автоматизации
производства, эффективное использование производственных площадей.
К недостаткам этого
способа относят сложность оборудования и трудность переналадки на выпуск
изделий другого вида.
При стендовом производстве изделия формуют в стационарных формах и
твердеют они на месте формования. Стендовые технологические линии целесообразно
использовать для изготовления крупноразмерных, особенно предварительно-напряженных
изделий, которые неэффективно изготовлять на поточно-агрегатных или конвейерных
линиях.
Таблица 8
Технико-экономические
показатели линий по производству стеновых панелей
Показатель
|
Конвейерная линия
|
Стендовая линия
|
Годовая производительность, м3
Число
работающих в две смены, чел
Съём с 1 м2 площади, м3
Годовая выработка на одного
рабочего, м3
Установленная мощность кВт+кВ·А
|
25000-35000
33
21,2
1560
241+75
|
12000-17500
21
5,6
664
205+182
|
По технико-экономическим показателям можно сделать вывод, что
производство стеновых панелей по конвейерной технологии намного эффективнее,
т.к. годовая выработка на одного рабочего почти в два с половиной раза выше, а
съём с 1 м2 площади почти в четыре раза выше по сравнению со стендовой
технологией.
Окончательно
применяем конвейерный способ производства
4.2
Укладка и уплотнение бетонной смеси
Укладка
и равномерное распределение бетонной смеси внутри форм – полуавтоматическое
управление. Бетоноукладчик СМЖ 166Б имеет бункера, установленные на раме,
которая может двигаться продольно; бункера двигаются поперечно по порталу,
имеется поворотная воронка с движением на 180°С, что позволяет распределять
смесь по поверхности изделия любого очертания. Непрерывную выдачу бетонной
смеси производят ленточными питателями.
Удобоукладываемость
бетонной смеси для изготовления наружных стеновых панелей должна составлять
5-10 секунд. Распределение и уплотнение бетонной смеси в форме осуществляется
посредством объёмного виброуплотнения. При таком уплотнении вибрационные
импульсы сообщаются всей бетонной смеси формуемого изделия в объёме формы.
Объёмное виброуплотнение осуществляется на виброплощадках с вертикально
направленными колебаниями с частотой 50 Гц.
Виброплощадка
– универсальное формовочное оборудование для формования широкой номенклатуры
изделий в передвижных формах с грузоподъёмность до 20 т. Виброплощадки
передвигают колебательные движения от рамы с вибровозбудителем к закреплённой
на нём форм со смесью. Рамы имеют упругие опоры и устройства для крепления форм
электромагнитным способом.
4.3
Тепловая обработка изделий
Эффективность
применения бетона в современном строительстве в значительной мере определяется
темпами производства железобетонных изделий. Решающим средством ускорения
твердения бетона в условиях заводской технологии сборного железобетона является
тепловая обработка.
Как известно, цикл тепловой обработки бетонных и
железобетонных изделий складывается из следующих периодов:
1) подъём
температуры;
2) изотермическое выдержка при наивысшей принятой температуре;
3) охлаждение
изделий.
1.
Период подъёма температуры.
Преждевременное
повышение температуры даже в условиях, исключающих возможность испарения влаги,
отрицательно отражается на конечной прочности бетона. Оптимальное время подъёма
температуры перед тепловой обработкой зависит от ряда факторов и оно тем
меньше, чем тоньше помол цемента, чем меньше в нем белита и чем выше
температура среды, в которой выдерживается бетон перед тепловой обработкой.
Постепенный подъём температуры не только повышает
прочность бетона, но и обеспечивает получение более устойчивых прочностных
показателей. За счёт нагрева скорость реакции гидратации цемента резко
возрастает и ускоряется структурообразование бетона.
Схватывание
бетона зависит не только от состава цемента и бетона, но и от температуры
окружающей среды. Чем выше В/Ц и подвижность бетонной смеси и ниже температура
среды, тем продолжительней подъём температуры. В зависимости от этих факторов
время подъёма температуры для бетонов на портландцементе может изменяться от 2
до 10 ч. В нашем случае подъём температуры продолжается в течении 1,5 часа до
температуры 80-85°С т.к. используется предварительный разогрев
керамзитобетонной смеси.
2.
Период изотермической выдержки
После подъема температуры до заданного максимума
следует период изотермического прогрева, когда изделие выдерживается при
требуемой постоянной температуре. В этот период необратимо фиксируются все те
дефекты структуры, которые приобрел бетон в период нагрева.
Однако температурное равновесие в этот период может
нарушаться вследствие экзотермии цемента. В этом случае происходят отдача тепла
от изделия в окружающую среду и испарение воды. Изменение влажностного
состояния и температуры изделия при тепловой обработке. В течение небольшого
промежутка времени вследствие экзотермического эффекта температура бетона
значительно возрастает и может превысить температуру среды. При этом максимальное
превышение температуры среды может достигать 6...8°С.
На данном этапе наблюдается наибольшая скорость
формирования бетона. Разность температуры и влагосодержания по сечению бетона в
этот период начинает уменьшаться и постепенно выравнивается, что значительно
улучшается условия структурообразования, кроме того, в это время идёт дальнейшая
гидратация цемента. Длительность периода определяется скоростью выравнивания
температурного поля в бетоне и кинетикой химических реакций и составляет 7,5
часов.
3.
Период охлаждения
При понижении температуры в тепловой установке в
период охлаждения температура бетона должна снизиться до температуры окружающей
среды.
В этот период бетон имеет большую температуру, и
внутреннее давление паров в изделии превышает давление паров окружающей среды.
За счет образовавшегося температурного градиента происходит интенсивное испарение
влаги из бетона. По мере охлаждения изделия и испарения влаги с поверхности
происходит миграция влаги из центральных участков изделия. Влага, удаляясь из
изделия в виде пара, образует каналы, которые идут во все стороны от
центральных участков изделия к периферии и соединяют между собой пустоты и
поры, образовавшиеся в процессе приготовления и укладки бетона. Вследствие
этого цементный камень имеет больше пор, и после тепловой обработки
характеризуется направленной пористостью. Продолжительность периода охлаждения
– 2 часа.
При выгрузке изделия из камеры температурный перепад
между поверхностью изделий и температурой окружающей среды не должен превышать
40°С [7].
В итоге, тепловая обработка наружных стеновых панелей
из керамзитобетона осуществляется насыщением пара в щелевой камере по следующему
тепловому режиму:
, ч (8)
где Т1 – время периода подогрева, ч;
Т2 –
время периода изотермической выдержки, ч;
Т3 –
время охлаждения, ч.
, ч
Данный тепловой режим обеспечивает минимальный расход
топливно-энергетических ресурсов.
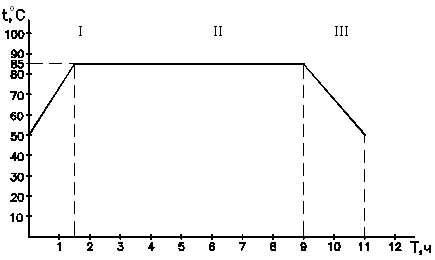
Рис.
2: График тепловой обработки
I период –
период подогрева; II период –
период изотермической выдержки; III период – период охлаждения.
Тепловлажностная
обработка оказывает существенное влияние на конечную прочность бетона. Следует
отметить что, такие факторы как: длительность предварительной выдержки,
водоцементное отношение, жесткость бетонной смеси, вид цемента должны всегда
учитываться при назначении режима тепловой обработки [7].
4.4
Отделка панелей
Формование наружных стеновых панелей по конвейерной
схеме осуществляется «лицом вниз». Декоративная отделка панелей производится
декоративным составом на основе мраморной крошки с размером частиц, до 10 мм, а
также ковровой керамикой.
Керамические
плитки подбираются по рисунку, наклеивается на бумажные листы и укладываются на
поддон форм-вагонеток. Облицовка крепится слоем цементно-песчаного раствора
толщиной 2 см, с подвижностью не более 1-2 см.
После
тепловой обработки, электромостовым краном стеновая панель устанавливается на
моечную машину, где производится отчистка поверхности от бумаги с помощью
горячей воды.
При
декоративной отделки стеновых панелей мраморной крошкой, отдельно
приготавливается фактурная бетонная смесь. После тепловой обработки стеновая панель
мостовым краном устанавливается на машину для обнажения фактурного слоя, где
обнажение производится при помощи абразивных дисков.
4.5
Описание производственного процесса
Для производства стеновых панелей применяется
конвейерный способ производства (рис. 3).
Форма-вагонетка с изделием извлекается из щелевой
камеры и устанавливается на передаточное устройство 9, при помощи которого
перемещается на пост №1, где производится отчистка бортов и вкладыша от
наплывов бетона, снятие вкладыша с формы и транспортировка его к месту складирования,
открытие бортов с помощью механизма открывания бортов СМЖ 3002.
На посту №1 работают 2 рабочих. На посту №2 оператор
проводит кантование формы с изделием. Изделия с помощью кантования СМЖ 3001Б
устанавливается в вертикальном положении и стропуется. Снятое с формы изделие
транспортируется на конвейер отделки и доводки стеновых панелей СМЖ-3100.
После
снятия изделия с поддона, рабочий преступает к очистки формы от наплывов
бетона, затем к нему подлючается оператор. Отчистка должна производиться
тщательно при помощи специальных скребков. После отчистки производится смазка
формы при помощи удочки-распылителя.
На
посту №4 постоянно работает оператор и рабочий. Они выполняют операции
укладывания в форму облицовочные коврики бумагой к поддону, разглаживают от
середины к краям. Во избежание смещения полотнищ относительно друг друга они
должны быть склеены внахлёст не менее 70-80 мм.
На
посту №5 рабочий данного поста и рабочий поста №4 устанавливают арматурный
каркас, а также фиксаторы для создания защитного слоя и предупреждения порыва
ковров арматурными стержнями.
Страницы: 1, 2, 3, 4, 5, 6
|