Курсовая работа: Червячный двухступенчатый редуктор
Условие прочности можно записать:

где S -
фактический коэффициент запаса; [S]=
2,5 - допускаемый коэффициент запаса.
Так как вал подвергается изгибу и кручению фактический
коэффициент запаса определяется по формуле:
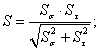
где Sσ
- коэффициент запаса прочности по нормальным напряжениям;
Sτ - коэффициент запаса прочности по касательным напряжениям.
Коэффициенты запаса прочности Sσ и Sτ
можно определить по формулам:
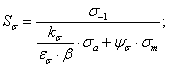 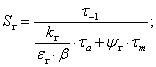
где σ-1 и τ-1 - пределы выносливости стали при
симметричном цикле изгиба и кручения;
kσ и kτ
- эффективный коэффициент концентрации нормальных и касательных напряжении;
εσ и ετ - масштабный коэффициент касательных
и нормальных напряжений;
σа и τа – амплитуда цикла нормальных и
касательных напряжений;
σm и τm
– среднее напряжение цикла нормальных и касательных напряжений;
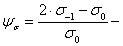
для углеродистых сталей, имеющих σB = 650 – 750 МПа; принимают для
легированных сталей для упомянутых выше сталей 
Выбираем в качестве материала вала:
Легированная сталь 40Х улучшенная (dвала до 120 мм), тогда σB = 930 МПа;
Определим σ-1 и τ-1:


Будем производить расчет для каждого из предположительно
опасного сечения. Примем, что нормальные напряжения от изгиба изменяются по
симметричному циклу, а касательные от кручения - по отнулевому (пульсирующему).
Осевой момент сопротивления (изгибу):
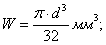
Полярный момент сопротивления (кручению):

Амплитуда и среднее напряжение цикла касательных напряжений:
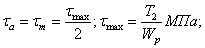
Амплитуда нормальных напряжений:
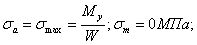
Построим эпюры моментов
для промежуточного вала. Для этого необходимо разбить вал на 3 участка и
определить на каждом момент в двух плоскостях, а затем найти суммарный момент.
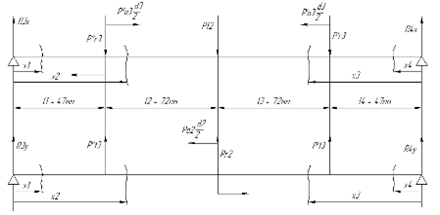
Рис. 8.1 Расчетная схема
промежуточного вала
Крутящий момент Mх
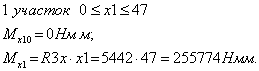

Нмм


Нмм;
Нмм.

Нмм;
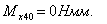
Изгибающий момент MY
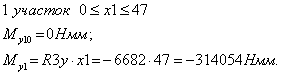

Нмм;
Нмм.

Нмм;
Нмм.

Нмм;
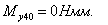
Суммарный изгибающий
момент:
;
Нмм;
Нмм;
Нмм;
Нмм;
Нмм;
0Нмм;
Нмм.
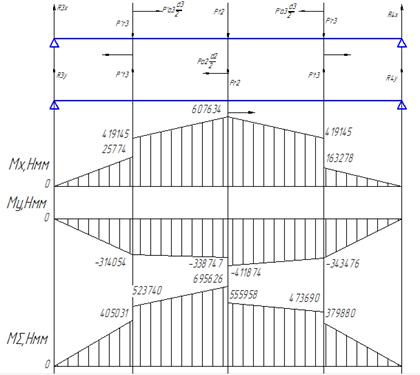
Рис. 8.2 Эпюры
изгибающего, крутящего и суммарного моментов
Расчет проведем в двух
наиболее опасных сечениях, т. е. в тех сечениях, где суммарный момент
наибольший. Первое сечение – МΣ = 695626 Нм, второе - МΣ = 523740 Нм.
Целью расчета является
определение коэффициента запаса прочности для проверки прочности вала. Величина
запаса прочности вала в опасном сечении должна превышать нормативное значение
запаса прочности, иначе произойдет усталостная поломка вала.
Условие прочности имеет
вид: S>[S],
где [S] – допускаемый коэффициент запаса
прочности, [S]=2,5.
Коэффициент запаса
прочности S определяется по формуле:
,
где - коэффициент запаса
прочности по нормальным напряжениям; - коэффициент запаса прочности по
касательным напряжениям.
,
где - предел выносливости, для
углеродистых конструкционных сталей вычисляется по формуле , возьмем Сталь 45: ; - эффективный
коэффициент концентрации нормальных напряжений(для  =1.75 [2, c 165 ]); -
масштабный фактор для нормальных напряжений ( =0,82 (0,835) для вала Ø 50
(45) мм [2, c 166]); - амплитуда цикла нормальных
напряжений, равная наибольшему напряжению изгиба в рассматриваемом сечении
 - среднее напряжение цикла
нормальных напряжений,
первое сечение: ;
второе сечение:
- коэффициент чувствительности
материала к асимметрии цикла, для углеродистых сталей .
,
где - предел выносливости стали при
симметричном цикле кручения, для конструкционных сталей ; - эффективный
коэффициент концентрации касательных напряжений ( для [2, c 165]); -
масштабный фактор для касательных напряжений ( (0,715)для вала Ø 50
(45)мм [2, c 166]); - амплитуда цикла касательных
напряжений, равная наибольшему напряжению изгиба в рассматриваемом сечении ; - среднее
напряжение цикла касательных напряжений; - коэффициент чувствительности к
асимметрии цикла для касательных напряжений, принимаем равным 0,1.
Рассмотрим первое сечение
– МΣ = 695626Нм.
Момент сопротивления
изгибу опасного сечения вала:
Амплитуда нормальных
напряжений изгиба в опасном сечении:
Коэффициент запаса
прочности по нормальным напряжениям:
Полярный момент
сопротивления опасного сечения вала:
Амплитуда и среднее
напряжение цикла касательных напряжений:
Коэффициент запаса
прочности по касательным напряжениям:
Результирующий
коэффициент запаса прочности для опасного сечения:
S = 6,6> [S] = 2.5, следовательно, условие прочности выполняется.
Рассмотрим второе сечение
- МΣ = 523740 Нм.
Момент сопротивления
изгибу опасного сечения вала:
Амплитуда нормальных
напряжений изгиба в опасном сечении:
Коэффициент запаса
прочности по нормальным напряжениям:
Полярный момент
сопротивления опасного сечения вала:
Амплитуда и среднее
напряжение цикла касательных напряжений:
Коэффициент запаса
прочности по касательным напряжениям:
Результирующий
коэффициент запаса прочности для опасного сечения:
S = 3,6> [S] = 2.5, следовательно, условие прочности выполняется.
9 ПРОВЕРОЧНЫЙ РАСЧЕТ ПОДШИПНИКОВ ВАЛОВ
Основными причинами
утраты работоспособности подшипников являются усталостное выкрашивание рабочих
поверхностей тел качения или беговых дорожек колец, их абразивный износ,
разрушение сепараторов, расклинивание колец и тел качения, образование
недопустимых пластических деформаций на беговых дорожках.
В данном курсовом проекте
рассматривается как основной вид разрушения – выкрашивание тел качения.
Признаками начала процесса усталостного разрушения (выкрашивания) деталей
подшипника являются повышение шумности, потеря точности вращения вала,
возникновение вибрации. Целью расчета является долговечность подшипников.
Под динамической
грузоподъёмностью С радиально-упорных подшипников понимают постоянную нагрузку,
которую группа идентичных подшипников может выдержать в течении расчётного
срока службы
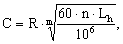
где Lh – ресурс
подшипника; n – частота вращения данного из колец подшипника; С – динамическая
грузоподъёмность; m – показатель кривой выносливости, для шариковых m=3 и для
роликовых m=10/3.
Ресурс подшипника :
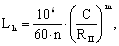
где Rп – приведённая
нагрузка на подшипник.
Приведённая нагрузка для
радиально-упорных подшипников рассчитывается по следующей формуле :

где X и Y – коэффициенты
радиальной и осевой нагрузок; Rr и Ra – радиальная и осевая нагрузки
подшипника; V – коэффициент вращения; Кs - коэффициент безопасности; Kт – температурный коэффициент.
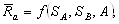
где Ra – полная осевая
нагрузка; SA и SB – внутренние осевые силы; А – внешняя осевая нагрузка.
Под статической
грузоподъёмностью Со радиально-упорных подшипников понимают такую радиальную
нагрузку, которой соответствует общая остаточная деформация тел качения.
Значение Со указываются в
каталогах.
При выборе подшипника
должно выполняться условие :

где Ро – приведённая
статическая нагрузка.
При совместном действии
на подшипник радиальной Rr и осевой Ra нагрузок приведённая нагрузка
определяется как большая из расчётов последующим формулам :
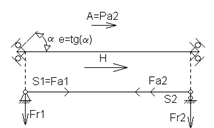
Рис. 9.1 Схема действия сил
,
где Xo и Yo –
коэффициенты радиальной и осевой статических нагрузок.
Таблица 9.1
Исходные данные для
расчета на ЭВМ
Эксплуатационные
параметры |
Требуемый
ресурс (час.) |
3000 |
Режим
нагружения |
типовая
циклограмма нагружения
кафедры
"Детали машин" СПбГТУ №8
|
Конструктивные
параметры подшипниковых опор |
Валы |
Б |
П |
Т |
Частота
вращения вала (об./мин.) |
1421 |
40,6 |
10 |
Относительно
нагрузки вращается |
Внутреннее
кольцо подшипника |
Коэффициент
безопасности |
1.30 |
Температурный
коэффициент |
1.00 |
Валы |
Б |
П |
Т |
Внешняя
осевая сила |
3570 |
697 |
0 |
Радиальные
нагрузки |
687 |
8618 |
6946 |
1321 |
8082 |
6324 |
Подшипники
в опорах 1 и 2 |
разные |
одинаковые |
одинаковые |
|
|
|
|
|
|
|
|
Результаты расчета
Быстроходный вал
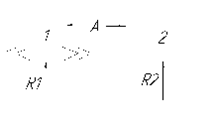
Рис. 9.2 Схема нагружения
опор быстроходного вала
Опора 1 2
Подшипник 7307
307
Радиальная реакция, Н 687
1321
Максимальная осевая
реакция, Н 7140 0
Статическая
грузоподъемность, Н 76000 18000
Эквивалентная статическая
нагрузка, Н 16154 2642
Ресурс при вероятности
безотказной работы 0.9, ч 6540 100000
Вероятность безотказной
работы при заданном ресурсе 0.968 0.999
Промежуточный вал
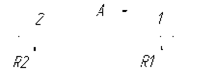
Рис. 9.3 Схема нагружения
опор промежуточного вала
Опора
Подшипник 46308 46308
Радиальная реакция, Н 8082
8618
Максимальная осевая
реакция, Н 10992 12444
Статическая
грузоподъемность, Н 30100 30100
Эквивалентная статическая
нагрузка, Н 16164 17236
Ресурс при вероятности
безотказной работы 0.9, ч 50200 37200
Вероятность безотказной
работы при заданном ресурсе 0.998 0.998
Тихоходный вал
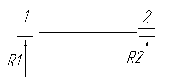
Рис. 9.4 Схема нагружения
опор тихоходного вала
Опора 1 2
Подшипник 213 213
Радиальная реакция, Н 6946
6324
Максимальная осевая
реакция, Н 0 0
Статическая
грузоподъемность, Н 34000 34000
Эквивалентная статическая
нагрузка, Н 13892 12648
Ресурс при вероятности
безотказной работы 0.9, ч 100000 100000
Вероятность безотказной
работы при заданном ресурсе 0.999 0.999
Расчеты показывают, что
все подшипники удовлетворяют условию долговечности, т.е. расчетный ресурс
работы превышает требуемый.
10
РАСЧЕТ СОЕДИНЕНИЙ ВАЛ-СТУПИЦА
Целью расчета являются
конструктивные размеры шпоночного соединения. Величина расчетных напряжений
смятия на рабочих поверхностях шпонок при передаче вращающего момента не должна
превышать допускаемых значений, иначе произойдет смятие рабочих поверхностей
шпонок. Также касательное напряжение среза не должно превышать допускаемых
значений.
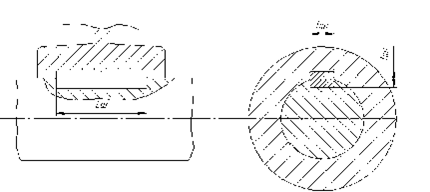
Рис. 10.1 Схема
шпоночного соединения
Выбираем следующие
призматические шпонки:
1) шпонка на быстроходном валу под шкив:
Шпонка 8х7х25 ГОСТ 23360-78;
2) шпонка на промежуточном валу под
червячное колесо и шестерни:
Шпонка 20х12х80 ГОСТ
23360-78;
3) 2 шпонки на тихоходном валу под
зубчатые колеса и 1 шпонка под муфту:
Шпонка 20х12х50 ГОСТ
23360-78;
Материал шпонок Сталь 45.
Напряжение смятия должно
удовлетворять условию:
,
где допускаемые
напряжения смятия [sсм]=120 МПа, dв- диаметр вала, Т – передаваемый крутящий момент.
1)
2)
3)
Проверка на срез
проводится по условию:

Допустимое напряжение среза 
1) 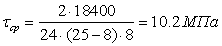 ;
2) МПа ;
3) МПа .
Все шпонки удовлетворяют
условиям прочности на смятие и срез.
11
ПРОВЕРОЧНЫЙ РАСЧЕТ МУФТЫ ВЫХОДНОГО ВАЛА
Задачей данного раздела
является выбор муфты и проверка её на прочность.
Если при соединении
входного вала редуктора с валом двигателя можно конструктивно обеспечить все
уровни установочной регулировки, причем жестко и стационарно, то при соединении
выходного вала редуктора с входным валом транспортера обеспечить быструю и
точную регулировку невозможно, так как редуктор и транспортер имеют разные
основания. Из-за этого очень трудно и нерационально обеспечивать точную
соосность и параллельность валов. Исходя из этого, необходимо применить муфту,
которая смогла бы компенсировать эти недостатки.
Из предложенных стандартных муфт выбрана зубчатая муфта по ГОСТ
50006-83, которая обладает достаточной жесткостью, высокой нагрузочной
способностью, способностью компенсации относительно небольших смещений осей
валов. К достоинствам также можно отнести технологичность - использование для
нарезки зубьев стандартного зуборезного инструмента.
Один из вариантов исполнения зубчатой муфты – двухвенечная
зубчатая муфта. Она состоит из двух втулок с внешними зубьями и соединенных
болтами двух обойм с внутренними зубьями. Обоймы соединены с помощью болтов
посаженных в отверстия без зазора. Большое число одновременно работающих зубьев
эвольвентного профиля обеспечивает компактность и высокую нагрузочную
способность муфты. При вращении валов в случае их перекоса происходит
циклическое смещение зубьев втулок относительно обойм. Это смещение вызывает
изнашивание зубьев - основную причину их повреждения. Для снижения потерь на
трение и увеличения долговечности зубьев зубчатого зацепления предусматривают
его работу в масляной ванне, используются масла повышенной вязкости.
Типоразмер муфты
определяется исходя из Трасч = 1,4*Твых= 1,4*1350=1750 Н×м.
После определения типоразмера, исходя из значения момента на
выходном валу редуктора Тт, производится выбор основных параметров зубчатого
зацепления и геометрии муфты. Затем находится диаметр расположения болтов:

и сила, действующая на каждый болт:

где: D1 и D - диаметры фланцев, зависящие от
типоразмера муфты, мм;
z - число болтов
Тр.рас = К*Т3 = 1,2Тт, К = Кδ*Кσ = 1* 1,2 = 1,2.
Кδ =1,0. . . 1,5 - коэффициент безопасности (характер
последствий при выходе из строя)
Кσ= 1 ,0 ... 2,0 - коэффициент динамичности (характер
нагрузки).
Определяются диаметры болтов, установленных без зазора:
,
где [τ] - допускаемое касательное напряжение, МПа.
С целью предупреждения недопустимой интенсивности изнашивания
предусматривают снижение уровня напряжений смятия, величину которого
устанавливают расчетом.
,
где:
zm - число зубьев;
bm - ширина зуба,
мм;
h = 1.2 mm - рабочая высота зуба, мм;
dm - диаметр делительной окружности зубчатого колеса, мм;
Kh - коэффициент неравномерности распределения нагрузки;
[σсм] - допускаемое напряжение смятия, МПа, зависящее от
вида термообработки;
[σсм] =5.. 7 МПа закалка до 40-45 НRС
[σсм] - 12 МПа термохимическая обработка до 55-60 ИКС
тт - модуль,
мм.
В соответствии с
минимальным диаметром выходного вала редуктора d =60 мм и действующим на нем моментом Трасч =1750 Н×м Нм, выбираем муфту по ГОСТ 50006 -
83, способную передавать вращающие моменты до 3150 Н.
Т,
Н×м
|
d,мм |
D,мм |
D1, мм |
D2, мм |
bm, мм |
zm, мм |
mm,мм |
z |
До3150 |
60 |
220 |
150 |
90 |
20 |
40 |
3 |
6 |
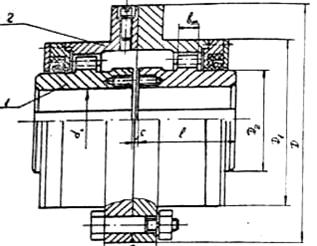
Рис. 11.1 Зубчатая муфта
Характеристики:
Сила:
.
Класс прочности болтов 6,6 из стали 35Х, для которых σВ =
600 МПа,
σТ =0,6 600 = 360 МПа, а [τ] = 0.3 360 = 108 МПа.
Диаметры болтов равны:
.
Конструктивно принимаем болт с резьбой М12. Для муфт с
жесткими обоймами Kh -1,1 ,
[σсм]=10..12 МПа термохимическая обработка до 55 - 60 НRС.
Осуществим проверку работоспособности зубьев муфты по
напряжениям смятия:
МПа < [σсм]
Условие прочности на
смятие выполняется.
Проверочный расчет болтов
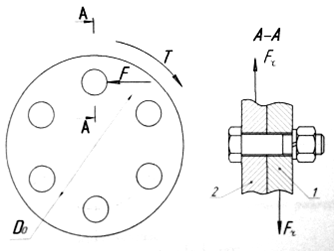
Рис. 11.2 Расчетная схема
болтового соединения
Расчет болта, нагруженного поперечной силой Fr при установке его с зазором. Для обеспечения
неподвижности фланцев 1 и 2 болт затягивают силой затяжки F3.
6 болтов d =12
мм уставлены с зазором. Момент на муфте:
Трасч = 1,4*Твых= 1,4*1350=1750*103Н×мм.
Рассчитаем болты на статическую прочность:

сдвигающая сила,
z - число болтов;
d - диаметр болта с зазором;
[τ] = 40МПа - допускаемое касательное напряжение.
, усилие затяжки:
.
, где [S] – 1,5 – коэффициент запаса
Возьмем класс прочности болтов 5,8:
σт = 400 МПа
[σ] = 267 МПа
.
Условие прочности выполняется.
12 ТЕПЛОВОЙ РАСЧЕТ РЕДУКТОРА
Задачей данного раздела является определение рабочей
температуры редуктора.
Необходимо проверить
условие:
где Dt – фактический перепад температур, °С; [Dt] – допускаемый перепад температур, °С.
Из уравнения теплового
баланса получаем:
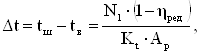
где tш – температура масла, °С; tв – температура окружающего воздуха, °С; N1 – подводимая мощность, равная 1954,5 Вт; hред – КПД редуктора, hред=0,82;
Kt=15-17 – коэффициент теплоотдачи; Ар –
площадь теплоотдающей поверхности корпуса редуктора, м2.
Определим площадь
поверхности Ар:
Ар= 2LB+2ВН+2LH =2×0,340×0,500+2×0,500×0,400+2×0,340×0,400=0,93 м2,
где L – длина редуктора,500 мм;B – ширина редуктора,340 мм; H – высота редуктора,400 мм.
Вычислим Dt:
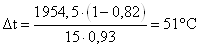
Dt<[Dt]=60°C, следовательно, условие выполняется,
редуктор работает без перегрева.
13 ВЫБОР СМАЗОЧНЫХ МАТЕРИАЛОВ
Смазывание зубчатых,
червячных передач и подшипников уменьшает потери на трение, предотвращает
повышенный износ и нагрев деталей, а также предохраняет детали от коррозии.
Снижение потерь на трение обеспечивает повышение КПД редуктора.
По способу подвода
смазочного материала и зацеплению различают картерное и циркуляционное
смазывание.
Зубчатые колёса смазывают
окунанием, погружая их в масло. Заливка масла производится через смотровую
крышку, а слив – через сливную пробку. Для контроля уровня масла используется
жезловый маслоуказатель.
Для смазывания
подшипниковых узлов применяется пластичный смазочный материал. Для защиты
подшипниковых узлов от вымывания пластичной смазки жидкой, используются мазеудерживающие
кольца. В качестве уплотнений на валы предусмотрены манжеты резиновые
армированные.
Скорость скольжения у
червячной передачи: 3,8 м/с.
Контактные напряжения у
червячной передачи 326 МПа.
Для червячной передачи
кинематическая вязкость .
Окружная скорость у
зубчатой передачи 0,18 м/с.
Контактные напряжения у
зубчатой передачи 954 МПа.
Для зубчатой передачи
кинематическая вязкость .
Для смазывания передач
червячно-цилиндрического редуктора выбираем марку масла И-50А (кинематическая
вязкость )
[2, cтр.253].
Для смазки подшипников
будем использовать пластичный смазочный материал ПСМ Литол-24.
ЗАКЛЮЧЕНИЕ
На основании технического
задания был разработан силовой привод намоточного устройства.
Конструкция привода
включает асинхронный электродвигатель 4А90L2, клиноременную передачу с натяжным
устройством, горизонтальный цилиндрический двухступенчатый редуктор и литую
плиту. Конструктивной особенностью спроектированного редуктора является
раздвоение потока мощности на тихоходной ступени, при симметричном расположении
колес относительно опор, что улучшает условия работы зубчатых передач и
разгружает подшипники от действия осевых нагрузок. Для выравнивания потоков
мощности и обеспечения самоустановки колес тихоходный вал установлен в
«плавающих» опорах. С целью получения наиболее рациональной компоновки
проектируемого редуктора энерго-кинематический расчет привода, а также расчеты
зубчатых передач проводились для нескольких вариантов разбивки общего
передаточного отношения. Выбранный в качестве базового вариант обеспечивает
наряду с минимальной металлоемкостью наименьшие габаритные размеры редуктора,
необходимую плавность работы.
В процессе проектирования
диаметры ступеней валов редуктора определялись по результатам проектных
расчетов с последующей конструкторской проработкой. Проверочный расчет
промежуточного вала показал, что условие циклической прочности выполняется. Для
соединения валов с колесами и полумуфтами использованы стандартные
призматические шпонки, проверочные расчеты которых подтвердили их
работоспособность.
Подшипники качения
выбирались в соответствие с посадочными диаметрами валов в зависимости от типа
и «быстроходности» зубчатых передач. В конструкции «плавающих» опор были
использованы радиальные шарикоподшипники. Результаты проверочных расчетов
показали, что выбранные подшипники обладают достаточным ресурсом.
Редуктор имеет литой
разъемный корпус, верхняя и нижняя части которого соединяются посредством
болтов.
Силовой привод
монтируется на литой плите, крепящейся к бетонному основанию болтами.
Предварительное натяжение ремней клиноременной передачи осуществляется путем
перемещения электродвигателя относительно салазок посредством винта.
Смазывание зубчатых передач
и подшипниковых узлов осуществляется раздельно. Для смазки зубчатых передач
применяются смазочные шестерни. Уровень масла контролируется маслоуказателем.
Для залива масла и осмотра зубчатых передач в крышке корпуса предусмотрен
смотровой люк. Слив отработанного масла осуществляется через маслосливное
отверстие в картере, закрытое резьбовой пробкой. Подшипники качения смазываются
пластичной смазкой, набивка которой осуществляется при помощи пресс-масленок. В
целях предохранения пластичной смазки от вымывания подшипники внутри корпуса
защищены мазеудерживающими кольцами.
ЛИТЕРАТУРА
1. Дунаев П. Ф., Леликов О.П.
Конструирование узлов и деталей машин. М.: Высшая школа, 1985.
2. Чернавский С.А. Курсовое
проектирование деталей машин . М.: Машиностроение , 1988.
|