Дипломная работа: Влияние кристаллографической текстуры на анизотропию физико-механических свойств деформированных полуфабрикатов из сплавов на основе титана
Одновременно необходимо отметить, что
вследствие большей чистоты и гомогенности электрошлаковый металл склонен к
росту зерна в большей степени, чем электродуговой. Это следует учитывать при
разработке режимов нагрева металла под деформацию, а также условий его
охлаждения после деформации.
Существенно увеличивается длительная
прочность металла после ЭШП. Переплав стали, обеспечивая повышение ее чистоты
по включениям и газам, снижение серы, улучшает свариваемость. Институт
электросварки им. Е. О. Патона на основании обширных исследований показал
перспективность применения процесса ЭШП для улучшения свариваемости трубных
нержавеющих сталей, используемых в тепло- и атомной энергетике. ЭШП также
значительно улучшает полируемость нержавеющих сталей. Важным преимуществом ЭШП
является сохранение физико-механических свойств для нержавеющих сталей
переходного класса.
В последние годы большое распространение получают комплексные
методы получения высококачественных сталей, в которых используются сразу
два-три переплава. В ряде случаев сталь выплавляют методом ВИП с последующим
ЭШП или ВДП. Плавка в индукционных вакуумных печах обеспечивает глубокую
дегазацию и высокую степень раскисления в результате электромагнитного
перемешивания и длительного воздействия вакуума. Новые методы плавки и их
сочетания позволяют резко повысить металлургическое качество нержавеющих
сталей, использовать новые композиции легирующих элементов и практически решить
все задачи, которые ставят машиностроители перед металлургами. [8]
3.2 Выплавка аустенитных азотсодержащих коррозионно-стойких
сталей
Использование азота в качестве легирующего элемента широко
известно и реализуется различными производителями для получения стали,
предназначенной для работы в сложных условиях. Однако механизм ввода азота в
сталь в сравнении с механизмом ввода других легирующих элементов имеет ряд
специфических особенностей и до сих пор представляет значительный интерес с
точки зрения изучения закономерностей поведения азота и разработки относительно
дешевого способа производства стали с гарантированным уровнем содержания азота.
Применение электрошлакового переплава приводит к получению
слитков, в значительной степени лишенных сегрегаций легирующих элементов,
ликваций и других дефектов макроструктуры. Это ведет к тому, что по прочности и
ударной вязкости сталь ЭШП имеет заметное преимущество перед сталью открытой
выплавки при сохранении высоких пластических характеристик.
Для получения в стали азота на уровне 0,30-0,50%
обязательно ее легирование большим количеством элементов, повышающих
растворимость азота в жидком и твердом растворах, а именно – хромом, марганцем,
ванадием и ниобием. Одновременно, с той же целью, сталь должна содержать
минимально необходимое количество никеля, меди, кремния и других элементов,
снижающих растворимость азота.
К последней группе относится также углерод, необходимость
снижения которого до минимальных значений связана не только с его отрицательным
влиянием на растворимость азота в стали, но и с обеспечением высокой
коррозионной стойкости и благоприятной структуры металла.
При разработке технологии производства коррозионно-стойких
азотсодержащих сталей, особое внимание должно быть обращено на следующие
основные положения процесса выплавки и разливки металла:
- выбор шихтовых материалов и легирующих элементов и раскислителей;
- проведение окислительного периода и температурного режима с
учетом введения большого количества присадок для обеспечения заданного химического
состава, в том числе по содержанию углерода и азота;
- рафинировка и шлаковый режим;
- порядок ввода легирующих элементов для обеспечения
максимального усвоения азота из азотированных материалов.
При выплавке стали в завалку необходимо использовать только
углеродистые отходы известного химического состава, обеспечивающие низкую массовую
долю цветных и вредных примесей. Все легирующие элементы и раскислители должны
иметь сертификаты качества и строго им соответствовать. Известь должна быть свежеобожженной.
Для обеспечения лучшего усвоения и уменьшения времени
рафинировки феррониобий, феррохром и металлический марганец нужно присаживать в
печь в прокаленном виде.
Учитывая низкое содержание углерода и фосфора в готовой
стали, необходимо использовать металлический марганец Mn 965 с содержанием
углерода не более 0,10%, и феррохром содержанием фосфора не более 0,02%, а
также использовать для легирования металла азотом азотированный феррохром с
содержанием азота не менее 6%.
По расплавлению металла необходимо производить продувку металла
кислородом. В процессе продувки необходимо окислить не менее 0,4% углерода.
Окислительный период необходимо заканчивать при содержании углерода не более
0,02% и фосфора не более 0,008%.
Окислительный шлак необходимо скачивать до появления зеркала
металла.
Температура металла в конце окислительного периода должна
быть не ниже 1640°C.
После скачивания окислительного шлака также необходимо провести
предварительное раскисление металла кусковым алюминием на штангах в количестве
1,5-2,0 кг/т и кусковым 75 % ферросилицием из расчета введения кремния на
0,40-0,50% без учета угара и навести рафинировочный шлак смесью свежеобожженной
извести, плавикового шпата и шамота. После проплавления шлаковой смеси надо производить
присадку дробленого феррохрома в несколько приемов в прокаленном виде (до
красного свечения). По расплавлению последней порции феррохрома надо скачать
шлак и навести новой шлаковой смесью из свежеобожженной извести и плавикового
шпата в соотношении 4:1.
После проплавления шлаковой смеси присадить металлический
марганец в несколько приемов.
Феррониобий и феррованадий присаживать после ферромарганца не
позднее, чем за 10 минут до выплавки.
Азотсодержащие материалы для лучшего усвоения азота
присаживать в несколько приемов при температуре металла не более 1580°C. Окончательное раскисление стали
производить кальцийсодержащими материалами. Температура металла в ковше перед
разливкой 1490-1520оС.
Сифонную разливку проводить с максимальной скоростью в
крашеные изложницы с защитой струи металла аргоном. Слитки передавать на ковку
горячим садом.
Выплавку стали производят в электродуговой печи. Шихтовку
плавки составляют с использованием отходов, химический состав которых должен
быть обеспечивать ориентировочную расчетную массовую долю хрома перед продувкой
металла кислородом 5-6% и чистого железа, обеспечивающего низкую массовую долю
серы и фосфора в металле.
После продувки металл раскисляют присадкой кускового алюминия
2-3 кг/т, а шлак порошком алюминия до разжижения, и присаживают расчетное
количество хрома и феррониобия (никель-ниобиевой лигатуры).
Для предотвращения науглероживания металла в процессе
проплавления феррохрома, его присадку производят отдельными порциями в 2-3
приема.
После расплавления последней порции феррохрома шлак
скачивают, раскисляют металл металлическим кальцием и алюминием и присаживают
азотированный марганец и азотированный феррохром на ориентировочное содержание
1,0-1,2% азота. [9]
3.3 Термомеханическая обработка аустенитных
коррозионно-стойких сталей
Для удаления поверхностных дефектов
используются три вида ремонта: а) обдирка поверхности слитков на токарных
станках; б) полная или выборочная местная зачистка поверхности слитков с
помощью абразивных станков; в) огневая зачистка поверхности слитков с помощью
специального резака.
Обдирку поверхности слитков
производят при наличии массовых дефектов глубиной до 10—15 мм. Этот метод
позволяет надежно удалять большинство дефектов и получать качественную
поверхность проката. Недостатком метода является перевод большого количества
металла в стружку, низкая производительность токарных станков (даже при
оборудовании их несколькими резцами).
Однако для некоторых
трещиночувствительных сталей обдирка является единственно приемлемым способом
ремонта слитков. Зачистка поверхности слитков на абразивных станках позволяет
производить удаление отдельных дефектов и благодаря этому сокращать затраты
труда и металла. Зачистке следует подвергать некоторые прочные марки
нержавеющих сталей. Для слитков, предназначенных для прокатки или продольной
ковки, глубина зачистки дефектов допускается до 20—50 мм (в зависимости от
сечения) с развалом 1:6. Для кузнечных слитков, которые подвергаются осадке,
глубина выточек ограничивается до 30 мм при развале 1:10.
Весьма часто сочетают обдирку на
токарных станках с последующей абразивной зачисткой оставшихся поверхностных
дефектов либо обдирку наиболее пораженной дефектами зоны и местную зачистку
дефектов в остальной части слитка.
Огневой зачистке обычно подвергают
крупные листовые слитки нержавеющей стали, глубина дефектов у которых более 5 мм, и их общая площадь занимает более 1/3 грани. Такую зачистку осуществляют на специальных
открытых участках с помощью газовых резаков.
Для развития высокой температуры в
зоне реза металла к головке резака по питательным штангам подводят природный
газ и кислород (около 99% О), а также порошковую смесь: на два объема порошка
силико-кальция один объем порошка ПАМ-4. При сгорании в кислороде порошка ПАМ-4
(50% А1 и 50% Mg) развивается температура около
2500°С, что обеспечивает плавление тугоплавких элементов, входящих в состав
нержавеющей стали.
Отрицательным моментом в абразивной и
огневой зачистке металла является получение немобильных отходов металла с
потерей ценных легирующих элементов.
Как правило, нержавеющие стали
обладают пониженной пластичностью, т.е. пониженной способностью деформироваться
без разрушения. Пластичность стали зависит от ее природы, характера
напряженного состояния при деформации, а также температурных и скоростных
условий деформации.
Наибольшее влияние на горячую
пластичность оказывает химический состав стали, определяющий ее свойства и
фазовый состав при деформации. Образование избыточных фаз различного состава,
находящихся в металле в виде включений, прослоек и пленок, существенно
затрудняет протекание процесса пластической деформации. В этой связи влияет и
ликвация химического, а следовательно, и фазового состава металла в слитке.
Выбор оптимального химического
состава стали даже в пределах марки, подавление процесса ликвации при разливке,
диффузионное выравнивание состава при термообработке или нагреве под прокатку
являются существенными условиями повышения пластичности металла. К природе
стали следует также отнести ее микросостав: с одной стороны, наличие вредных
элементов— цветных металлов: свинца, цинка, висмута, сурьмы, олова, мышьяка и
др; с другой — наличие поверхностно активных элементов в определенных дозах:
бора, кальция, магния, церия и других РЗЭ.
Микросостав стали определяется
составом шихтовых материалов, методом и технологией выплавки, составом
футеровки печи и оказывает существенное влияние на поведение металла при
деформации. Например, если удаление ряда цветных металлов при вакуумном дуговом
и электроннолучевом переплавах положительно сказывается на уровне пластичности,
то испарение магния может привести к ухудшению способности к деформации.
Большое влияние на пластичность оказывают температурно-скоростные
условия, при которых осуществляется деформация металла. В большинстве случаев с
повышением температуры пластичность металла возрастает, сопротивление
деформации уменьшается, повышается производительность станов. В связи с этим
обычно стремятся деформировать металл при более высоких температурах.
Однако для нержавеющих сталей при
выборе температуры нагрева и деформации следует учитывать не только опасность
пережога, но и фазовое состояние металла, рост зерна и т. п. факторы,
существенно влияющие на горячую пластичность и свойства прокатанной стали.
Повышенным сопротивлением деформации
обладают стали с наибольшей легированностью аустенита, особенно содержащие
интерметаллидные соединения и карбиды вольфрама и молибдена.
Сопротивление деформации зависит от
температуры: и с понижением оно увеличивается. Верхний предел температуры
деформации определяется температурой перегрева и пережога стали, которая на
100—200 град ниже температуры плавления стали, и кривой пластичности стали.
Если сталь обладает высокой температурой начала рекристаллизации, то
ограничивают и температуру конца прокатки (ковки). Она должна быть выше
температуры рекристаллизации, так как при снижении температуры происходит
упрочнение стали рост сопротивления деформации.
Для многих нержавеющих сталей
необходимо производить деформацию в узком интервале температур, но при этом
нежелательно применять малые обжатия по проходам, так как большое число
проходов ведет к ухудшению качества металла.
Станы для прокатки нержавеющих сталей
должны учитывать эти особенности и иметь повышенные прочность и мощность
двигателя: контрольно-измерительная аппаратура должна обеспечить высокую
точность температурного режима нагрева. [7]
3.4 Термомеханическая обработка аустенитных азотсодержащих
коррозионно-стойких сталей
Введение в коррозионно-стойкие
аустенитные стали большого количества азота, который превосходит по упрочняющей
и аустенитнообразующей способности другие легирующие элементы, позволяет
создать новые немагнитные сплавы с высокими механическими свойствами и
сопротивлением коррозии. Такие сплавы не содержат других (кроме азота)
γ-стабилизаторов (Ni, Мn, Сu, Со), а также дорогих и дефицитных легирующих добавок,
входящих в состав традиционных аустенитных коррозионно-стойких сталей (Mo, W, Nb или Ti). Например, сплавы, содержащие 21 -24 % Сr и 1,0 - 1,4 % N после нагрева до
температуры, достаточной для растворения нитридов хрома в γ-твердом
растворе, и охлаждения в воде обладают сочетанием высокой прочности (σ02
=850-900 МПа), пластичности (δ=25-30%, ψ=35-40 %) и износостойкости.
По абразивной износостойкости эти сплавы в 2 - 3 раза превосходят известную
сталь 110Г13Л, а по стойкости против межкристаллитной коррозии — сталь типа
08Х18Н10Т
Существенным недостатком
высокоазотистых Fe-Сr-N-сплавов, как и известных сплавов систем Fe-Cr-Mn-N, Fe-Cr-Ni-N и Fe-Cr-Mn-Ni-N, является их склонность к выделению
нитридов хрома при температурах 500-900°С по механизму прерывистого распада.
Это проявление нестабильности аустенита выражено тем более резко, чем выше
степень пересыщения γ-твердого раствора азотом. Прерывистый распад такого
твердого раствора с высоким содержанием никеля и марганца происходит с
образованием перлитоподобных колоний, состоящих из аустенита с равновесным
содержание азота и пластинчатых частиц нитрида хрома типа Cr2N. В Fe-Сr-N-сплавах пересыщенный азоте аустенит или мартенсит при
указанных выше температурах распадается с образованием ферритно-нитридной
структуры.
Развитие прерывистого распада в
высокоазотистых сплавах приводит к неоднородности механических свойств деталей,
имеющих большие сечения, также к значительному снижению одновременно прочности,
пластичности, вязкости, коррозионной стойкости и ухудшению свариваемости.
Способы устранения отрицательного влияния прерывистого распада на эти свойства
рассмотрены в работе. Наиболее эффективным из них является проведение холодной
пластической деформации со значительными степенями обжатия (не менее 50 %),
создающей высокую плотность дефектов кристаллического строения и, как следствие
этого, изменение формы характера распределения нитридных частиц, формирующихся
при последующих термических воздействиях. Холодная пластическая деформация Fe-Сr-Mn-N- или Fe-Сr-Ni-Мn-N-сплавов методами
прокатки, волочения или гидроэкструзии с суммарной степенью обжатия 60 - 80 %
обеспечивает повышение их прочности (до σв =2000-3000 МПа в
зависимости от конечных размеров сечения образцов или изделий).
Другим возможным способом устранения
прерывистого распада высокоазотистых сплавов является горячая пластическая
деформация (при прокатке суммарная степень обжатия не менее 80 %) с окончанием
при температурах, несколько превышают; температуру начала прерывистого распада,
но не достаточных для развития процесса собирательной рекристаллизации
аустенита. При горячей пластической деформации Fe-Сr-Мn-N- или Fe-Сr-Ni-Мn-N-сплавов (содержащих 0,6-1,0% N) прокаткой при 1000- 1100 °С с
суммарным обжатием 70 % формируется фрагментированная структура (с размером
ячеек 0,4-0,7 мкм), обеспечивающая сочетание высокой прочности (σ0,2
=800-1000МПа), пластичности (δ=30-50%), и ударной вязкости (KCU= 0,8-1,4 МДж/м2). [11]
Лист толщиной 20мм, полученный из «огарка» (часть электрода
не подвергшийся ЭШП) имел предел текучести 560-770МПа и ударную вязкость
113-135Дж/см2, а лист 20 мм (ЭШП) имел предел текучести787-918МПа и
ударную вязкость 172-215Дж/см2.
3.5 Термообработка аустенитных азотсодержащих
коррозионно-стойких сталей
Термическая обработка нержавеющих
сталей аустенитного класса сравнительно проста и заключается в закалке в воде с
1050—1100°С. Фактически это отжиг на гомогенизацию (гомогенизационный отжиг) с
охлаждением в воде – аустенитизация.
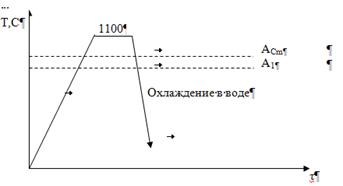
Рис. 10. Схема закалки нержавеющей стали
Нагрев до этих температур вызывает
растворение карбидов хрома (М23С6), а быстрое охлаждение
фиксирует состояние пересыщенного твердого раствора. Медленное охлаждение
недопустимо, так как при этом, как и при отпуске, возможно выделение карбидов,
приводящее к ухудшению пластичности и коррозионной стойкости. Кроме того, при закалке
происходят рекристаллизационные процессы, устраняющие последствия пластической
деформации, которой часто подвергаются нержавеющие аустенитные стали.
Механические свойства аустенитных нержавеющих
сталей в закаленном (смягченном) состоянии характеризуются низким значением
предела текучести, невысокой прочностью и очень высокой пластичностью.
Очевидно, что этот способ упрочнения
применим лишь для так видов изделий, как тонкий лист или лента, проволока и т.
п. [7]
Изменяя режимы термической обработки
высокоазотистых хромистых сталей, можно влиять на фазовые и структурные
превращения при нагреве и охлаждении сталей и как следствие на их свойства.
Фазовые превращения, происходящие при нагреве сталей с аустенитной структурой,
связаны с образованием нитридов, начинающимися при ~500°С (зонная стадия) и
заканчивающимися при ~730°С (стадия выделений). Нитриды, обеспечивающие высокую
твердость стали, весьма дисперсны и имеют вид тонких реек. Коагуляция нитридов
при 700-800°С приводит к резкому снижению твердости. После выдержки при 950-1050°С твердость
закаленных сталей достигает величины, близкой к твердости закаленной
высокоуглеродистой стали с 0,6-1,0% С.
В процессе охлаждения (его скорость в
наших экспериментах составляла 120°С/мин.) сталей происходит γ→α
-превращения по двум механизмам:
- диффузионному (при 680°С), с
распадом обедненного азотом аустенита на феррит с крупными зернами
полиэдрической формы и нитриды хрома;
- мартенситному, с образованием
пластинчатого мартенсита из обедненного азотом аустенита.
При повышении температуры нагрева
предварительно закаленных сталей температура начала мартенситного превращения
снижается. Например, для стали, содержащей 18% хрома и 0,9% азота, после
нагрева до 900, 1100 и выше 1150°С γ→α превращение по
мартенситному механизму протекает при температурах 305, 110°С и ниже комнатной
соответственно. Чем выше температура нагрева под закалку, тем большее
количество нитридов растворяется, что приводит к уменьшению количества α-
фазы и понижению твердости. [5]
Термическая обработка листа толщиной 10мм показала
возможность снятия избыточного наклепа и повышения ударной вязкости. Полученные
значения предела текучести и ударной вязкости составили соответственно
670-770Мпа (вместо 920-990МПа до термической обработки) и 280-325Дж/см2
(вместо 135-160Дж/см2 до термической обработки).
Радикальный способ упрочнения
аустенитных сталей — холодный наклеп; при деформации порядка 80—90 % предел
текучести достигает 980—1170 МПа, а предел прочности 1170—1370 МПа при
сохранении достаточно высокой пластичности. [7]
Глава 4. Свойства аустенитных азотсодержащих
коррозионно-стойких сталей
В настоящее время в химической
промышленности находят применение хромоникелевые стали типа 18-12 и 20-20
(иногда легированные 2—3% Мо) с крайне низким содержанием углерода — не более
0,03% (в отдельных случаях не более 0,02%). Эти стали не склонны к
межкристаллитной коррозии в ряде весьма агрессивных сред и их не требуется
стабилизировать титаном или ниобием. Однако из-за малого содержания углерода и
повышенной склонности к рекристаллизации такие стали обладают пониженным
пределом текучести в сравнении с классическими нержавеющими сталями, имеющими и без того невысокий предел текучести. С целью
повышения прочностных свойств малоуглеродистых нержавеющих сталей без ущерба
для коррозионной стойкости их легируют азотом в небольших количествах, что
вызывает упрочнение за счет растворения азота в γ-твердом растворе.
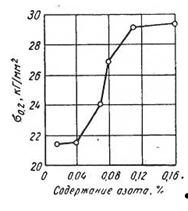
Рис. 11. Влияние растворенного азота
на предел текучести (σ0,2) стали.
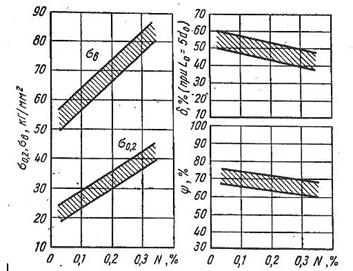
Рис. 12. Влияние азота на
механические свойства малоуглеродистых аустенитных сталей Cr-Ni, Cr-Ni-Mo и Cr-Ni-Mn-Mo сталей типа
18-10, 18-14-3 и 20-12-10-3
Влияние азота, растворенного в
γ-твердом растворе, на изменение механических свойств ряда хромоникелевых,
Сr— Ni — Мо и Сr — Ni — Мn сталей иллюстрируют рис. 11 и 12, из рассмотрения которых
следует, что упрочнение пропорционально содержанию азота, растворенного в
стали. Для стали Х18Н10 при 0,02% С и 0,15% N предел текучести достигает 30 кГ/мм2.
Количество растворенного азота в свою очередь тем больше, чем выше концентрация
хрома и марганца. Упрочнение, связанное с растворением азота в твердом
растворе, вызывает незначительное уменьшение пластичности и ударной вязкости аустенитных
сталей в отличие от дисперсионно-твердеющих сталей, в которых упрочнение
сопровождается значительной потерей вязкости. В γ-твердом растворе стали
00ХТ5НТ4АМЗ, закаленной после аустенитизации при температуре 1050°С, может быть
растворено до 0,20% N, а в случае
дополнительного легирования марганцем (сталь 00Х18Н12Г10АМЗ) в твердом растворе
растворяется до 0,34% N . Следует, однако, учитывать, что растворимость азота в
твердом растворе и в расплаве различна, поэтому фактическое содержание азота в
стали зависит от условий выплавки, разливки, кристаллизации слитка и других
факторов.
Азот, находящийся в γ-твердом растворе низкоуглеродистых
хромо-никелевых сталей типа 18-12, не ухудшает их общей коррозионной стойкости
в кипящей 65%-ной HNO3 и не ухудшает поведения металла
после провоцирующего отпуска в критическом интервале температур. Понижая
содержание углерода, можно достигнуть существенного улучшения коррозионной
стойкости стали с повышенными прочностными свойствами. Так, уменьшение
содержания углерода в стали 00Х18Н14АМЗ (0,18% N) с 0,047 до 0,015% приводит к увеличению, минимального
времени до возникновения склонности к межкристаллитной коррозии с 30 мин до
1000 ч при испытании по методу AM
(рис. 13).
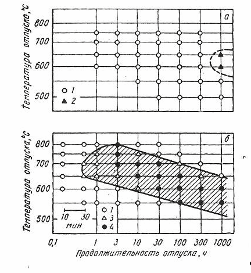
Рис. 13. Результаты испытаний на межкристаллитную коррозию
хромоникельмолибденовых сталей с содержанием 0,015 и 0,047% С, а также с
повышенным содержанием азота в кипящем растворе сульфата меди в серной кислоте:
1 – коррозия отсутствует; 2 — коррозия на глубину до 0,05 мм; 3 — слабая коррозия; 4 — сильная коррозия
Содержание, % |
|
C |
Si |
Mn |
Cr |
а |
0,015 |
0,5 |
1,39 |
17,53 |
б |
0,047 |
0,46 |
1,50 |
17,97 |
|
Ni |
Mo |
N |
а |
13,97 |
2,87 |
0,182 |
б |
14,97 |
2,81 |
0,184 |
На примере стали 00Х18Н14АМЗ можно
также сделать вывод, что в небольших количествах азот не оказывает
отрицательного влияния на поведение однофазной аустенитной стали в условиях
коррозии под напряжением в кипящем 42%-ном растворе хлористого магния. С учетом
области разброса (рис. 14) предел длительной коррозионной прочности образцов с
0,04 и 0,16% N практически одинаков.
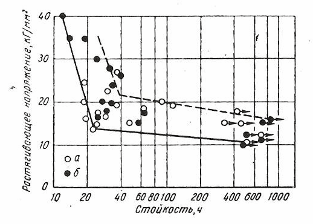
Рис. 14. Результаты испытаний на
коррозионное растрескивание под напряжением Сr — Ni —
Мо сталей с присадкой и без присадки азота в кипящем 42% -ном растворе
хлористого магния. Поверхность образцов электрополирована и пассивирована в 15%
-ном растворе азотной кислоты в течение 1 ч при 40°С. Стрелкой отмечено
появление отдельных надрывов
Содержание, % |
|
C |
Si |
Mn |
Cr |
а |
0,024 |
0,4 |
1,42 |
17,64 |
б |
0,030 |
0,42 |
1,23 |
18,50 |
|
Ni |
Mo |
N |
а |
14,40 |
2,98 |
0,04 |
б |
14,07 |
2,97 |
0,16 |
В малоуглеродистой хромоникелевой
стали, легированной азотом, наличие стабильной аустенитной структуры и отсутствие
второй фазы исключает опасность структурно-избирательной коррозии и делает
сталь не подверженной охрупчиванию при отпуске в интервале температур
600—900°С. Подобные стали хорошо полируются в противоположность титан
содержащим нержавеющим сталям, обработка которых затруднена из-за образования
скоплений или больших размеров карбонитридов.
Для сварки сталей, не подвергаемых дальнейшей термообработке,
могут быть использованы аустенитные присадочные материалы из Сr — Ni—Мо сталей, а для сварки конструкций, подвергаемых
термообработке, используют присадочный материал, содержащий примерно 0,03% С,
18% Сr, 14% Ni, 10% Мn,
2,5% Мо и 0,2% N. [6]
Выводы
На основе проведенного выше анализа
литературы можно сделать вывод, что использование ЭШП эффективно для выплавки
азотсодержащих коррозионно-стойких аустенитных сталей. Свойства, получаемые
после проведения ЭШП намного выше, чем после проведения только электродуговой
плавки. Формируемый при ЭШП слиток, за счет направленной кристаллизации в
водоохлаждаемом кристаллизаторе, обработке химически активным шлаком и
затвердеванию в шлаковом гарнисаже, характеризуется высокой однородностью
структуры, высокой плотностью, низким содержанием неметаллических включений,
вредных примесей и гладкой поверхностью, не требующей дополнительной
механической обработки. За счет однородной структуры, получаемой при ЭШП,
получаем однофазную аустенитную структуру с низкой магнитопроницаемостью (μ
≤ 1,01 Гс/Э). В сталях полученных электродуговой плавкой с последующей
прокаткой возможно большие включения ферритной составляющей (особенно при
недостатке марганца). Макроструктура слитков ЭШП характеризуется высокой
плотностью и однородностью, что, естественно, обеспечивает высокое качество
деформированного металла даже при малых степенях деформации.
Для слитка ЭШП характерно очень
равномерное и дисперсное распределение второй фазы, например, первичного
феррита, боридной или карбидной эвтектики в аустенитной основе.
Список использованной литературы
1. Банных О.А., Блинов В.М., Деркач Г.Г., Колесников А.Г.,
Костина М.В., Петраков А.Ф., Семенов В.Н. Научные основы создания нового
поколения сталей и сплавов для эксплуатации в экстремальных условиях и
технологии их обработки. Москва 2000 г.
2. Б. Е. Патон, Б.И. Медовар, Г.А.Бойко. Электро-шлаковая
технология. Общество «Знание» украинской ССР Киев – 1976 г.
3. Гуляев А. П. Металловедение. Москва «МЕТАЛЛУРГИЯ» 1986 г. 541 с.
4. О. А. Банных, В. М. Блинов. Дисперсионно-твердеющие немагнитные ванадийсодержащие
стали. Издательство «Наука», 1980г.
5. Химушин Ф.Ф. Нержавеющие стали. Государственное
научно-техническое издательство литературы по черной и цветной металлургии.
Москва 1963 г. 600 с.
6. М. В. Приданцев,
Н. П. Талов, Ф. Л. Левин Высокопрочные аустенитные стали. М.: изд.
«Металлургия», 1969, с. 248.
7. Г.М. Бородулин, Е. И. Мошкевич. Нержавеющая сталь. Москва «МЕТАЛЛУРГИЯ»,
1973г. 319с.
8. В. И. Коротич С.Г. Братчиков. Металлургия черных металлов.
Москва «МЕТАЛЛУРГИЯ», 1987г. 239с.
9. Журнал Современная электрометаллургия №2 2008 г. А.Митчелл Кристаллизация металла в процессах переплава. с. 4-12.
10. Журнал Металловедение и термическая обработка металлов №1
2002 г. Костина М.В., В.М. Дымов., Банных О.А., Блинов В.М. Влияние
пластической деформации на структуру и свойства высокоазотистых сплавов системы
Fe – Сr
11. Журнал Металловедение и термическая обработка металлов №7
2001 г. Костина М.В.,
Банных О.А., Блинов В.М. Влияние пластической деформации и термической
обработки на структуру и упрочнение азотистой стали 0Х16АН4Б
12. А. Д. Крамаров. Производство стали в электропечах.
Издательство «МЕТАЛЛУРГИЯ» Москва 1969 г. 350 с.
13. И. И. Новиков. Теория термической обработки металлов.
Москва «МЕТАЛЛУРГИЯ» 1986 г. 479 с.
|