Курсовая работа: Расчет, выбор и обоснование посадок соединений редуктора
Назначаем шероховатость сопрягаемых поверхностей шпонки, вала
и втулки Ra = 3.2 мкм, а несопрягаемых
поверхностей- Ra=12,5 мкм. Выбираем по экономические
методы окончательной обработки деталей соединения: шпонка -шлифование плоское
получистовое; паз вала - фрезерование чистовое концевой фрезой; паз втулки -
протягивание чистовое.
Эскизы нормального шпоночного соединения, его деталей, схема
расположения полей допусков на размер b приведены дальше. Для обеспечения взаимозаменяемости шпоночного
соединения допуск на ширину паза следует рассматривать как комплексный, в
пределах которого находятся как отклонения ширины паза, так и отклонения его
расположения. Ограничение всех этих отклонений в пределах допуска на ширину
паза вала достигается контролем комплексными и элементными калибрами. Контроль
элементными калибрами производится до контроля комплексными калибрами.
На заводах автотракторного и сельскохозяйственного
машиностроения контроль деталей шпоночных соединений производит с помощью
предельных калибров.
Ширину пазов вала и втулки проверяют пластинами, имеющими
проходную и непроходную стороны. Размер от образующей цилиндрической
поверхности втулки до дна паза (d + t2) контролируют пробкой со ступенчатым выступом.
Глубину паза вала проверяют кольцевыми калибрами
-глубиномерами; симметричность расположения паза относительно осевой плоскости
проверяют у втулки пробкой со шпонкой, а у вала - накладной призмой с
контрольным стержнем.
При ремонте машин можно использовать как универсальные
средства измерения, так и калибры. Из большого числа размеров шпоночного
соединения за счет пластических деформаций изменяется только ширина шпоночных
пазов и ширина самой шпонки. Поэтому при дефектации можно использовать
универсальные средства измерения, а при восстановлении желательно применять
предельные калибры.
1.3 Выбор посадок для шлицевых соединений
Вместо шпоночного соединения (зубчатое колесо-вал) назначить шлицевое
соединение (зубчатое колесо-вал). Обосновать метод выбора центрирования,
системы посадок. Определить предельные отклонения выбранных полей допусков
центрирующих и не центрирующих параметров; рассчитать предельные зазоры в
соединениях и результаты свести в таблицу.
Построить схемы расположения полей допусков и эскиз шлицевого соединения
и его деталей в поперечном сечении.
В данное время применяют три способа центрирования сопрягаемой втулки и
вала: по наружному диаметру D, по внутреннему диаметру d и по боковым
поверхностям шлицов b.
Выбор способа центрирования определяется эксплутационными требованиями и
технологическими факторами.
Основным мотивом при выборе центрирования по D или d
является возможность наиболее производительно и экономично провести обработку
посадочных поверхностей. Центрирование по b применяется
крайне редко.
Поскольку предполагается, что в нашем соединении шестерня неподвижна то
наиболее экономически выгодно принять центрирование по D.
Находим [Sf] по формуле
= £[ cm] ([3],
стр. 53)
[Sf]=
[Sf]= 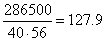
Принимаем по таблице 4.5 ([3]) , стр 60) Sf=127.9 .
Следовательно данное шлицевое соединение относится к лёгкой серии,
нормальные размеры соединения: 8 52 58;
Так как соединение неподвижно, то выбираем метод
центрирования по диаметру D. Для
размеров D и b выбираем поля допусков и посадки по таблице 4.72 ([2] , стр
252)
Для D , для b .На не центрирующий диаметр втулки d=42
мм назначаем по таблице 4.75 ([2] , стр 253 ) поле допуска H11
не центрирующий d вала по таблице 4.71 ([2] , стр 250) d³d1=40.4 мм.
D-8 52 58 9 .
Значение предельных значений отклонений размеров (D,b,d) шлицевого
соединения определяем по таблице 1.28 , 1.36 ([1]).
Шероховатость поверхностей для центрирующих (D и b) и
не центрирующих (d) элементов соединения назначаем в соответствии с
принятыми методами окончательной механической обработки по таблице 2.68 ([1]).
Вычисляем предельные зазоры в соединениях по центрирующим и не
центрирующим поверхностям.
Установленные размеры характеристики деталей шлицевого соединения,
шероховатость поверхностей и методы механической обработки сводим в таблицу 4.
Таблицa 4-Размерные характеристики и методы механической
обработки деталей шлицевого соединения D-8 52 58 9
Номинальный размер и поле допуска |
Предельные размеры, мм |
Допуск размера, мм |
Шероховатость поверхности, мкм |
Метод обработки |
max |
Min |
Отверстие втулки шлицевой |
58,03 |
58 |
0,03 |
RA=1.25
|
Протягивание чистовое |
Вал шлицевой |
57,97 |
57,94 |
0,03 |
RA=1.25
|
Шлифование чистовое |
Ширина впадины втулки шлицевой |
9,035 |
9,013 |
0,022 |
|
Протягивание чистовое |
Толщина шлицов вала |
8,987 |
8,965 |
0,022 |
RA=1.25
|
Шлицестрогание |
Нецентрирующие элементы |
Отверстие втулки шлицевой |
52,19 |
52 |
0,19 |
RA=6,3
|
Зенкерование чистовое |
Вал шлицевой |
52 |
50,4 |
1,6 |
RA=6,3
|
Шлицестрогание |
Рассчитываем предельные зазоры по
центрирующим параметрам D
Smax=ES-ei=+0.03-(-0.06)= 0.09мм.
Smin=EI-es=0-(-0.03)=0.03мм.
по размеру b:
Smax=EI-ei=+0.035-(-0.035)=0.070мм.
Smin=EI-es=0.013-(-0.013)=0.026мм.
по размеру d:
Smax=ES-ei=0.150-(-1.6)=1.75мм.
Smin=EI-es=0мм.
Контроль шлицевых соединений осуществляется комплексными и
поэлементными методами, пробковыми и кольцевыми калибрами контролируется взаимное
расположение поверхностей соединения.
Поэлементный контроль охватывает диаметры валов, отверстий,
толщину зубьев и ширину впадины отверстия. Поля допусков. Назначенные на
элементы деталей шлицевого соединения и указанные в условном обозначении,
контролируют в условном обозначении, контролируют независимо друг от друга
специальными гладкими калибрам.
2. ВЫБОР ПОСАДОК РАСЧЕТНЫМ МЕТОДОМ
2.1 Расчёт и выбор посадок с натягом
Вместо шпоночного соединения зубчатое колесо вал рассчитать и выбрать
посадку с натягом. Построить схему расположения функциональных полей допусков
деталей сопряжения. Вычислить эскизы размеров, назначить шероховатость
сопрягаемых поверхностей.
Определяем по формулам (1.115) и (1.116) ([1] , стр. 336) величину
наибольшего допускаемого давления на сопрягаемых поверхностях детали: втулки:Pдоп
D=0.58GTD[1-( )2]d=80
мм
Вала Рдоп d=0/58GTd[1-( )2]d2=53 мм
Принимаем для деталей сталь 45: GTD=353 МПа GTd=353 МПа; md=mD=0.3; E=2*105 МПа;
Pдоп D= МПа
Рдоп d= МПа
Чтобы в материалах вала и втулки не возникло пластических деформаций,
принимаем меньшее значение допускаемого давления:
Pдоп=125,1 МПа
Определяем величину наибольшего расчётного (допустимого) натяга по
формуле 1.117 ([1] , стр. 336)
Nmax p=Pдоп*d( );
Значение коэффициентов жесткости деталей вычисляем по формуле 1.111 ([1]
, стр. 334):
СD=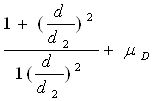
СD=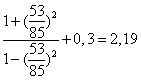
Сd=
Сd=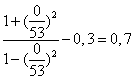
Nmax p= мкм
Определяем величину наибольшего функционального натяга по формуле:
Nmax f= Nmax p+U= Nmax f+5(RaD+Rad)
Nmax f=94+5(1,25+0,8)=107,25 мкм
Расчёт наименьшего функционального натяга определяем по формуле 1.107
([1] , стр. 333) величину наименьшего допускаемого давления на сопрягаемых
поверхностях деталей:
Pmin=
Pmin= МПа
Определяем по формуле 1.110 ([1] , стр. 334) величину наименьшего
расчётного натяга:
Nmin=Pmin*d( )
Nmin= мкм
Определяем по формуле Nmin f= Nmin p+U
величину наименьшего функционального натяга.
Nmin f=Nmin f+5(RaD+Rad)
Nmin f=5.8+5(1,25+0,8)=16.03.
Выбор посадки.
По известным предельным функциональным натягам посадка выбирается так,
чтобы был обеспечен запас прочности при эксплуатации (Nз=Nmin-Nmin f) и
технологический запас прочности соединения (Nзс=Nmin f-Nmin).
Изобразим принципиальную схему полей допусков посадки с натягом в системе
отверстия. Указываем на схеме наибольший функциональный натяг Nmax f=107,25
мкм.
По таблице 1.30 ([1]) в 4….8 квалитетах подбираем поле допуска вала, у
которого es<107,25 мкм на минимальную из всех возможных
величин.
Выбираем посадку: Æ53 H8/s7
У которой Nmax =83мкм, Nmin=7мкм
Nзс=Nmax f-Nmax
Nзс=107.25-83=24.25 мкм
От нижней границы поля допуска вала (ei=мкм)
откладываем наименьший функциональный натяга (Nmin f=16.03мкм) и отмечаем этот
уровень как 57 мкм. Следовательно верхнее отклонение отверстия ES<57
мкм. По таблице 1.36 ([1]) подбираем поле допуска отверстия , у которого EI=0
, ES<57 мкм .
Принимаем поле допускаH8: отверстия Æ42H8(+0.039)
Nзе=Nmin f-Nmin
Nзе=16.05-7=9.03 мкм
Определяем коэффициент запаса точности выбранной посадки:

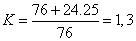
TN= Nmax-Nmin
TN=83-7=76
Рекомендуется значение К=1…2.Следовательно, посадка выбрана точно.
3. РАСЧЕТ И ВЫБОР ПОСАДОК ПОДШИПНИКОВ КАЧЕНИЯ
Для подшипникового узла быстроходного вала выбрать и обосновать класс
точности подшипника качения.
Установить вид нагружения внутреннего и наружного кольца.
По величине радиальной нагрузки рассчитать и выбрать посадку
для циркуляционно нагруженного кольца.
Выбрать и обосновать посадку местно или колебательно
нагруженного кольца.
Рассчитать предельные размеры деталей подшипникового узла,
предельные и средние натяги и зазоры в сопряжениях.
Построить схемы расположения полей допусков сопрягаемых деталей.
Выполнить проверку наличия радиального зазора в подшипнике после посадки
его на вал или корпус с натягом.
Определить шероховатость и допускаемые отклонения формы и
положения посадочных и опорных торцовых поверхностей заплечников вала и
отверстия корпуса.
Определить допуски соосности посадочных поверхностей вала и
корпуса.
Обозначить посадки подшипников качения на чертеже.
Вычертить эскизы вала и корпуса с обозначением допусков
размеров, формы, расположения, шероховатости посадочных и опорных торцовых
поверхностей.
Выбор и обоснование класса точности подшипников качения
Выбираем подшипник, исходя из формулы , так как передача
цилиндрическая, то следовательно . Выбираем шариковый
радиальный однорядный подшипник средней серии.
По таблице 16.3 ([3]) назначаем подшипник № 309.
Номинальные размеры подшипника: d=45мм;
D=100мм; В=25мм; r=2,5мм.
В редукторе сельскохозяйственных машин в основном применяются
подшипники качения 0 класса. Следовательно, принимаем класс точности подшипника
– 0.
Выбор вида нагружения внутреннего и наружного кольца.
Изучая конструкцию редуктора цилиндрического, устанавливаем, что кольцо
воспринимает радиальную нагрузку последовательно всей окружностью дорожки
качения и передаёт её также последовательно всей посадочной поверхности вала,
следовательно, внутреннее кольцо подшипника испытывает циркуляционный вид
нагружения.
Анализируя условия работы соединения, устанавливаем, что наружное
кольцо подшипника не вращается относительно действующей на него радиальной
нагрузки, следовательно, кольцо воспринимает нагрузку лишь ограниченным
участком окружности дорожки качения и передаёт её соответствующему
ограниченному участку посадочной поверхности корпуса. Такой вид нагружения
наружного кольца подшипника называется местным.
Расчёт и выбор посадки для циркуляционно нагруженного кольца
по величине радиальной нагрузки.
Выбор посадки для циркуляционно нагруженного кольца
производится по интенсивности радиальной нагрузки. Интенсивность радиальной
нагрузки определяется по формуле:
Страницы: 1, 2, 3, 4
|